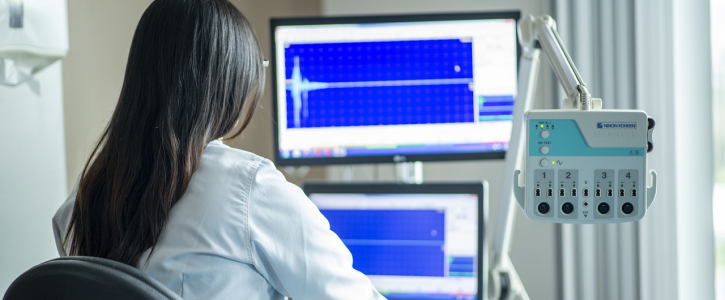
Printed circuit boards (PCBs) are key parts of many electrical devices, connecting critical components. Global demand for circuits has risen exponentially in recent years, and many less-than-reputable actors have entered the industry.
This guide explains common PCB issues (often found in circuits produced by less-experienced providers) and how to avoid them so the devices you use them in perform as intended, providing a high level of dependable service for years to come.
What Is PCB Failure?
PCB failure occurs for many reasons. The end result is that the PCB no longer functions as intended, which can lead to device breakdowns or complete failure. Because PCBs are used in many electronic devices that could malfunction in perilous situations, such as medical wearables, airplane, automobile, and hospital equipment, any possible issues must be identified and prevented — and when they happen, quickly fixed.
Any company looking to keep their electronics running smoothly can prevent PCB failure — and recover from it when it occurs — by understanding why it happens.
The complexity of the PCB design and manufacturing processes introduces many opportunities for issues to arise. Some failures result from design mistakes, such as inadequate clearances or incorrect measurements. Design errors can negatively affect the functioning of the products they’re used in. Others may be the result of issues in manufacturing, such as drilling errors or over-etching. Manufacturing mistakes often result in catastrophic consequences.
The good news is that most of these problems can be avoided by working with professionals who have a deep knowledge of the PCB design and development process and know about common PCB manufacturing problems and how to avoid them.
Following strict design and manufacturing rules and considerations can prevent component failure, connection issues, and other circuit board-related problems.
Here are some common things you may encounter if you work with less-than-reputable circuit manufacturers or those not experienced in your industry.
1. Plating Voids
Plated through-holes are copper-coated holes in a PCB. They allow electricity to move across the circuit. A PCB board fabricator drills holes through the circuit board to create them. Then, through an electroplating process, a layer of copper foil or a copper coating is added to the surface of the material and along the walls of the holes. This disposition process places a thin layer of electroless copper onto the circuit. Finally, additional layers of copper are added and etched to create the circuit image.
The deposition process is not a perfect one. Sometimes, it results in voids in the plating, which are gaps or holes. The plating voids are problematic because they prevent the electrical current from passing through the hole, making it ineffective.
The plating voids happen because of the following:
· Contamination
· Air bubbles in the material
· Inadequate cleaning of the holes
· Insufficient catalyzation of the copper in the deposition process
· Rough hole drilling.
Defects can be avoided by cleaning the material properly after drilling and closely following the manufacturer’s drill directions during use. You can avoid these issues by working with a well-qualified and experienced PCB manufacturing company.
2. Inadequate Copper-to-Edge Clearance
Copper is an incredibly conductive metal. It’s also relatively soft and vulnerable to corrosion. To prevent corrosion, the copper is covered with other materials.
The issue: when a PCB is trimmed, part of the coating can also be cut, exposing the copper below. This negatively impacts the board’s functionality, resulting in shorts and shocks.
This issue can be prevented by ensuring the space between the edge of the copper and the edge of the board (often referred to as the copper-to-edge or plate-to-edge clearance) meets the standards for the type of board being manufactured. A complete design for manufacturability (DFM) check by an experienced manufacturer like Tramonto Circuits typically identifies possible problems.
3. Poor Quality Soldering
Improper soldering during the PCB assembly process can result in significant consequences. One example of this can happen when a technician doesn’t heat the solder enough, referred to as cold soldering, which can result in circuit failure. In addition, when moisture enters the soldering process, it can contaminate the PCB pad and other components.
This contamination can cause PCB components to experience connection problems and possibly burn up. The best PCB manufacturers use visual or enhanced X-ray inspections to find bad soldering.
4. Slivers
Slivers are narrow wedges of copper or solder masks produced during printed circuit board manufacturing. These slivers are often created during the etching process.
The slivers can connect to other pieces of copper or expose copper plating that the solder mask should protect. The first issue can result in a short. The second can cause the copper to corrode over time. Both of these things can reduce the life of the circuit board.
Slivers can be prevented by designing boards with sections of minimum widths. A manufacturer can identify slivers with a DFM check.
5. Missing Solder Mask Between Pads
The solder mask is on top of the circuit board’s copper layer. It prevents the copper traces from accidental contact with other metal, solder, or conductive bits. It also acts as a barrier between the copper and the environment, which prevents corrosion and protects the circuit board’s handlers from electrocution.
In some circuit boards, the solder mask may be partially or entirely missing. This exposes the copper and can result in solder bridges forming between pins. When this happens, it can result in a short circuit and reduced corrosion protection, which can negatively impact the functionality and longevity of the PCB.
This defect is typically the result of a design oversight. The solder mask is undefined, or the settings for a larger board are carried over to a smaller one. This results in pad holes that are too large for the smaller printed circuit board.
All this can be prevented by checking the design before manufacturing, something a reputable manufacturer like Tramonto Circuits will do.
6. Acute Angles in Circuits
Acid Trap is the common term for acute angles in a circuit. The acute angles trap acid during the circuit board etching process. This allows the acid to build up in the corner of the angle, which keeps it there for longer than necessary. In this situation, the acid eats away more than intended, which can compromise a connection. This results in a defective circuit, which can cause severe problems in the future.
Experienced designers are aware of the issues related to acute angles and circuit boards. They are knowledgeable enough to avoid them.
7. Badly Manufactured Components
Another cause of printed circuit board failure happens when the engineering team uses poorly manufactured components. During the PCB production process, any physical damage because of the wrong components can harm the PCB, leading to power failure. Common circuit assembly defects and faults from poorly manufactured components include connection issues and loose parts. Also, residual flux (a substance used during soldering) left on a circuit panel can cause significant damage, making it necessary to repair the circuit board. Experienced manufacturers always use the right high-quality components in their PCBs.
8. Starved Thermals
Thermals are small traces surrounding pads. They’re used to connect pads to the plane. They allow the pads to disperse heat effectively and are critical for the soldering process.
Voids between the thermal and the rest of the plane — or the thermal and the pad — can lead to an incomplete connection. When this happens, it reduces the effectiveness of the heat transfer system the thermals create.
Starved thermals take much longer to transfer heat from pads to the rest of the plane, which can be problematic during soldering or if the circuit is under heat stress. A thermal pad with improper heat transfer may solder in an unusual way. It will also take unusually long to reflow, extending the assembly time. After manufacturing, circuit boards with starved thermals may deliver insufficient heat transfer and are often prone to overheating and heat damage.
The source of these issues can most often be traced back to the manufacturing process. These thermal connections are usually designed correctly in a computer-aided design (CAD) system but are somehow manufactured with a reduced connection to the plane. Manufacturing problems during thermal molding or machining, including over-machining or improper molding, can all lead to this issue. When it happens, it’s usually best to replace the thermal.
An experienced circuit manufacturing company like Tramonto Circuits can prevent faulty thermals, identify them when they happen, and replace them before any harm can occur.
9. Electromagnetic Issues
Electromagnetic compatibility and electromagnetic interference are two problem areas when it comes to circuit board design. Electromagnetic compatibility (EMC) is the generation, propagation, and reception of electromagnetic energy. Electromagnetic interference (EMI) is an unwanted effect of EMC that can cause damage. Too much EMI can cause products to react intermittently and not work as intended. It is typically the result of a design flaw.
EMI can be lowered by expanding the circuit board’s ground area and compartmentalizing the board and signals specifically for EMI. In addition, 90-degree angles must be avoided for most components because they can increase EMI interference. Also, use shielded cables during cable assembly and metallic packaging to absorb EMC and reduce EMI.
10. Environmental Contamination
Environmental factors can negatively impact PCB quality. PCBs exposed to dust, moisture, heat, and cold are likelier to fail. For instance, changes in temperature can make elements on the circuit contract or expand, which could damage or warp the soldering joints and boards themselves. Consulting with an experienced manufacturer like Tramonto Circuits can help mitigate these concerns before boards are fabricated.
Dust around a circuit board can build up over time, clogging the board, which can cause it to overheat. Also, moisture can result in corrosion, rust, and oxidation, damaging the PCB.
Plus 1: No or Inadequate DFM Check or Poor Communication
This guide reveals many things that can go wrong when designing and manufacturing PCBs. The good news is that all of them are preventable. That is why it’s so critical to partner with an experienced PCB manufacturer that runs DFM checks on the designs before they begin building them.
DFM is short for Design for Manufacturability.
DFM checking is the process of reviewing a circuit board layout to identify and minimize any issues that could occur during the fabrication and assembly process. DFM ensures that the design will result in a consistent product that performs as expected dependably. Unlike other standards that only consider how the PCB will potentially work, DFM looks at how the circuit board could break down.
Minimizing these issues requires a specific kind of expertise. Only a few of the design flaws covered in this piece are flagged by CAD software. That’s because it’s not designed to look for these possible issues. A sound DFM check, however, is focused on identifying these potential problems, drawing from an extensive and specialized database of design checks. All these checks may not apply to your specific circuit board, especially if it’s experimental. However, they’re critical to consider before manufacturing begins.
While DFM checks are a relatively common practice for most designers and manufacturers, many don’t understand or communicate design gaps properly. This can result in severe problems down the road.
That’s why you must partner with a custom PCB company like Tramonto Circuits that provides a thorough DFM check backed by a knowledgeable, communicative, and professional staff that will walk you through any issues that may arise with a circuit design or during the manufacturing process. Contact the experts at Tramonto today to find out how we can support you in developing circuits you — and your end users — can depend on.